

When I finished, I tightened everything up, put on and tensioned a blade, and then checked everything. The right thickness of washers to make the platform exactly lever was 0.1" Rear of the upper plastic blocks and the platform. Halves between the front of the lower plastic blocks and the platform and the other halves between the It tooks several tries and I ended up cutting 3/8" washers in half and inserting My solution to solve the problem was to insert shims between the platform and the plastic blocks that (In my opinion, all bandmills really should have bandwheel plumb adjustments and they also should have This seems to be a result of a combination of excessive clearance in the plastic blocks that travel the uprightsĪnd the lifting point of the platform being more toward the rear than in the middle.
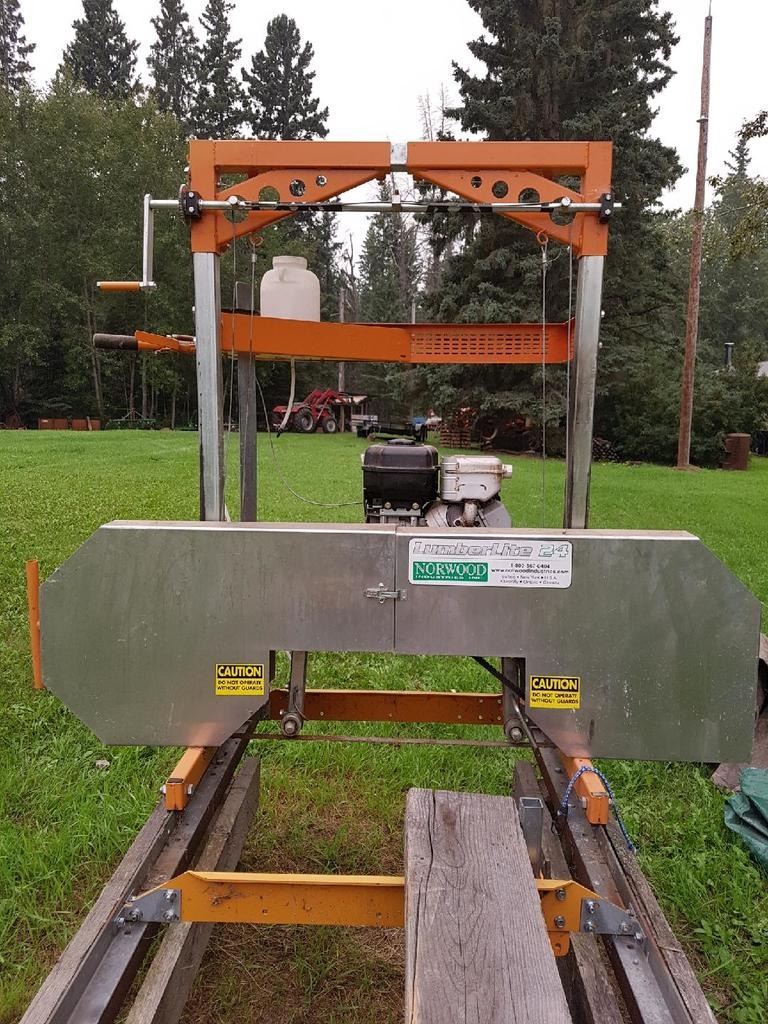
That it angles downward over 1/4", thus angling the bandwheels downward, thus angling the blade downward. But when the platform is raised (the cables areĪttached to the platform more toward back, away from the bandwheels, rather than in the middle), then it tilts so much It then is only slightly angled downward. I discovered that when the platform is all the way down, resting on its bottom with slack in the cables, that I then checked the uprights that the platform rides up and down on but they were exactly plumb. Over 1/4" from the back edge to the front edge. To check the level of the carriage platform itself and discovered that it too was angled downward Well, what do I do now there is no bandwheel plumb adjustment on the mill. The plumb of the band wheels and was surprised again to see that they were out of plumb,Īngled downward over 1/4" from top to bottom. Then I happened to think to check the blade itself for level and was surprised to see 4 & 1/2 turns seems about right, but I tried 4 turnsĪnd then 5 turns diving problem didn't go away.) (To tension the blade, Norwood recommends to turn the tensioning handle 4 & 1/2 turnsĪfter it contacts the tensioning spring. Then I tried more tension on the bladeĪnd then less tension same problem both ways. I tried a couple of new blades same problem. In the middle thickness being less than the thickness on the ends.Īt this point, I knew that I had to find out why the blade was diving in order to keepįrom continuing to mill boards that weren't consistent. The cant and cutting on the other side, thus the blade diving took place on both sides resulting The beams, however, were bowed inward on both sides due to cutting on one side and then flipping In the middle as the ends but showed a convex bow on one side and a concave bow on the other side. Previous cut matched the diving on the present cut. I then realized that the boards had a consistent thickness because the diving on the The wider the cut was, the more pronounced Thickness in the middle as the ends, I noticed that they all seemed to be bowed outwardĪ little on one side and bowed inward a little on the other side.īut it was the beams that I was cutting that were bowed inward on both sides and thus I then check a number of boards that I had previously cut and though most were the same The blade) it gradually rose back up to the original dimension". In other words, the blade was gradually diving to the middle of the cutĪnd then (because of the increasing pressure from the tension of Then I checked the 6" dimension and it also was gradually thinner in the middle than on the ends. Also, at 3' into the cutĪnd at 9' into the cut, it was about 9 & 7/8". I measured the 10" dimension and it wasĮxactly 10" on each end but in the middle it was less than 9 & 3/4". It was thinner in the middle than on the ends. So, I checked it with a string and sure enough, In the middle and not just on that one side, but on the other side as well. I noticed that it did not seem to be straight it seemed that it was bowed concave Then one day, as I was sighting down a 6"x10"x12' beam that I had just sawn, The boards always seemed to be the same thicknes end to end and side to side. I check the lumber frequently to see if it is sawing evenly. I have milled about 2 dozen logs thus far. I have the Norwood model LM29 sawmill I got it a couple months ago. (and it might apply to the other models as well), then you mightĬheck to see if you could be experiencing this same problem. If you have a Norwood sawmill, specifically the LM29 On the bandwheels, can cause the problem that I experienced. In the way the carriage is raised and that flaw, coupled with the lack of a plumb adjustment But I think that it has a definite design flaw I think they make a decent sawmill and there are a lot of featuresĪbout it that I like. Let me start by saying that this post is not meant to bash Norwood sawmills.
